Winner Best AI & Robotics Application 2024
Kaufland Stiftung
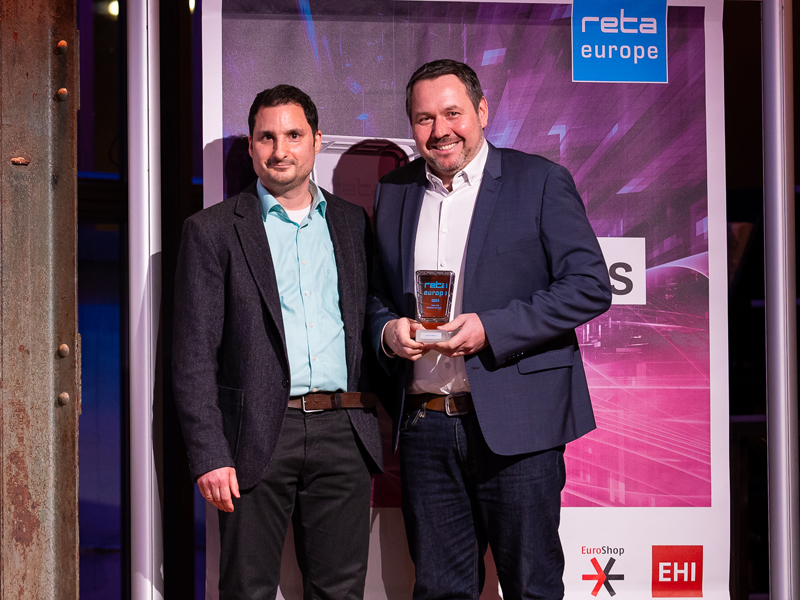
To counteract the difficulties of manual picking, particularly in the fruit and vegetable department, Kaufland has successfully introduced an automated picking system (AKA) in five out of six warehouses. The cardboard boxes are semi-automatically depalletised after goods receipt and the returnable crates are automatically depalletised and transported to a lane sorter as an intermediate buffer in flow lanes. Once the store order has been received, the mixed pallets are calculated using a packing pattern generator and released for picking. The system then transports the crates and cartons from the intermediate buffer to the semi-automatic picking workstations according to the order. For the reusable, clean mixed pallets, the crates are transported from the intermediate buffer to the automatic palletising robots. Once the mixed pallets have been formed, they are automatically transported to the staging lanes and from there manually directly to the loading gates. For carton picking, the system works according to the ‘goods to man’ principle and uses pulling and pushing instead of lifting to move the boxes. The focus here is on reducing the workload for employees, rapid availability for customers, reliability and scalability. It is flexible when processing reusable returnable load carriers (crates) and disposable cartons, which contributes to its efficiency and practicality.The technology service provider is BSS Bohnenberg GmbH.
Winner video
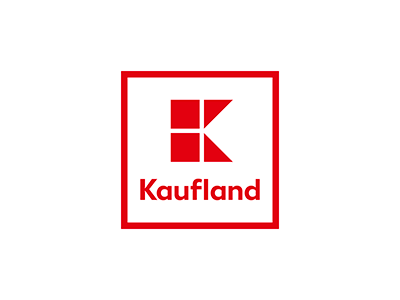
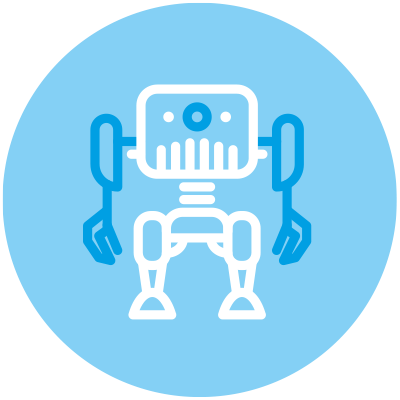
Best AI & Robotics Application
Kaufland Stiftung
Top Supplier Retail 2024
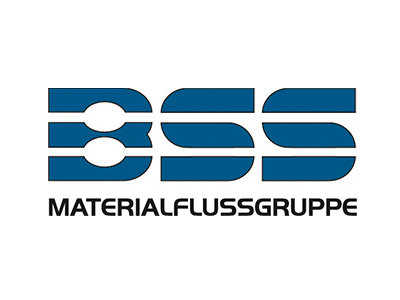
BSS Bohnenberg GmbH